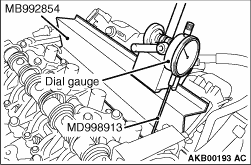
|
1.Install the special tool magnet base plate (MB992854) to the upper face of the cylinder
head at the inlet side. 2.Install the special tool dial gauge extension (MD998913) to the dial gauge. 3.When installing the dial gauge to the magnet base plate, the dial gauge must have
almost the same angle as the inlet valve has.
|
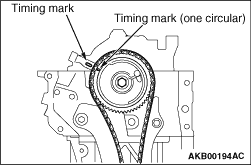
|
4.Rotate the crankshaft clockwise and align the timing mark of the rocker shaft holder with
the one circular timing mark of the V.V.T. sprocket. Therefore, the No. 1 cylinder is set at
the top dead centre on its compression stroke. 5.For the No. 1 cylinder inlet valve, adjust the valve clearance according to the following
procedures.
|
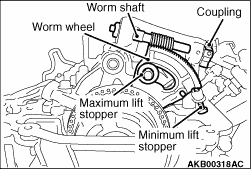
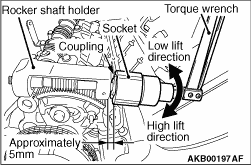
|
6.
caution |
- Never loosen the minimum lift stopper.
- When rotating the coupling, do not apply the torque more than 3 N·m to
prevent the damage.
- Do not forcibly push the worm wheel to the minimum lift stopper and the maximum
lift stopper.
- Never loosen the five Torx bolts at the upper portions of the rocker arm and camshaft
assembly.
|
Slowly rotate the coupling clockwise. When lightly touching the worm wheel to the minimum
lift stopper, stop the worm wheel at the position shown in the illustration.
note |
When rotating the coupling clockwise, the worm wheel should move in the minimum lift direction.
When rotating the coupling anti-clockwise, the worm wheel should move in the maximum lift direction.
|
note |
When manually rotating the coupling, insert a 12-point socket (24 mm) into the position
on the coupling approximately 5 mm away from the rocker shaft holder. Connect the mini torque
wrench and slowly rotate them.
|
|
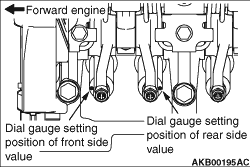
|
7.Set the dial gauge on the upper face of the valve spring retainer at the forward engine
side. Set the dial gauge to 0.
note |
As shown in the illustration, prevent the measurement error caused by the tilted valve,
install the rocker arm to the outside of the rocker arm.
|
|
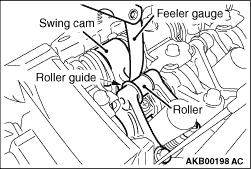
|
8.
caution |
- Straightly insert the feeler gauge in the vertical direction
not to touch the rocker arm roller guide.
- When inserting the feeler gauge too much, you cannot pull out the feeler gauge after
the adjustment. Do not insert the feeler gauge by more than 5 mm.
|
Between the swing cam and the roller of the rocker arm, insert the feeler gauge with 0.15
mm thickness, to approximately 5 mm from the top. Manually holding it, perform the adjustments
according to the following procedures.
note |
If the feeler gauge cannot be inserted between the swing cam and the roller of the rocker
arm, perform the adjustments according to the clearance adjustment procedures in the engine
adjustment. (Refer to GROUP 11C - On-vehicle Service - Valve Clearance Check
and Adjustment )
|
|
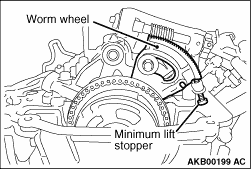
|
9.
caution |
Do not forcibly push the worm wheel to the minimum lift stopper.
|
Check the worm wheel stopping at the position as shown in the illustration, lightly touching
to the minimum lift stopper. At that time, manually hold the thickness gauge so that the thickness
gauge cannot excessively be inserted. 10.Loosen the rocker arm lock nut at the forward engine side. Pull up the adjusting screw
once. From the upper portion of the adjusting screw, sufficiently apply the engine oil between the
lower adjusting screw end and the valve axis end so that the engine oil can be provided enough.
And then, perform the adjustment by rotating the adjusting screw so that the dial gauge can
read -0.11 mm. 11.For the valve at the backward engine side, check the valve clearance in the same procedure
as that of the valve at the forward engine side. If the valve clearance is not within the standard
value, perform the adjustment in the same procedure as that of the valve at the forward engine
side. 12.After the adjustment, hold the driver to prevent the adjustment screw from rotating.
Tighten the lock nut to the specified torque. And then, check that the dial gauge reading does
not change. Tightening torque: 9.0 ± 1.0 N·m 13.Check again the valve clearance at the forward engine side. If the valve clearance
is not within the standard value, perform the adjustment in the same procedure as the first adjustment. 14.After the adjustment, hold the adjusting screw by the driver not to rotate the adjusting
screw. Temporarily tighten the lock nut. Rotate the coupling anti-clockwise and return the worm wheel
to the middle lift position. Pull out the thickness gauge. Specified torque: 9.0 ± 1.0 N·m 15.For the No. 2 cylinder inlet valve, adjust the valve clearance according to the procedures
from Step 7 to Step 14. 16.For the No. 1 and No.3 cylinder exhaust valves, adjust the valve clearance according
to the following procedures. 17.Insert the feeler gauge between the exhaust valve axis end and the adjusting screw.
Loosen the lock nut. Adjust the valve clearance so that the clearance is within the standard value
by rotating the adjusting screw. Standard value: 0.20 ± 0.03 mm 18.After the adjustment, hold the driver to prevent the adjustment screw from rotating.
Tighten the lock nut to the specified torque. Tightening torque: 9.0 ± 1.0 N·m 19.Rotate the crankshaft clockwise 1 revolution. Therefore, the No. 4 cylinder is set
at the top dead centre on its compression stroke. 20.For the No. 3 cylinder inlet valve, adjust the valve clearance according to the procedures
from Step 7 to Step 14. 21.For the No. 4 cylinder inlet valve, adjust the valve clearance according to the procedures
from Step 7 to Step 14. 22.For the No. 2 and No. 4 cylinder exhaust valves, adjust the valve clearance according
to the procedures from Step 17 to Step 18.
|