|
- Refer to Data List Reference Table
.
- Item 02: Crank angle sensor
|
| Q.
Is the check result normal? |
| Intermittent malfunction (Refer to GROUP 00 - How to Use Troubleshooting/Inspection
Service Points - How to Cope with Intermittent Malfunctions ).
|
| |
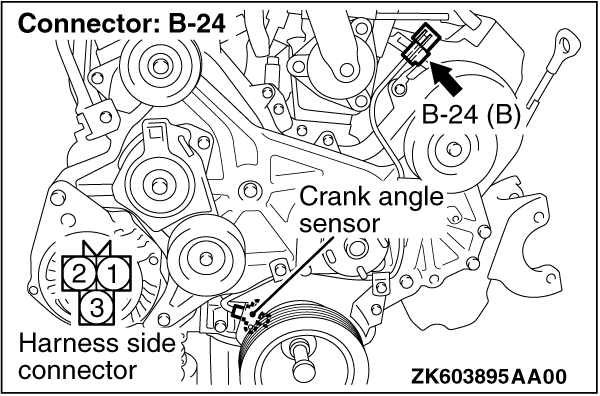
| Q.
Is the check result normal? Go to Step 3 .
Repair or replace the connector.
|
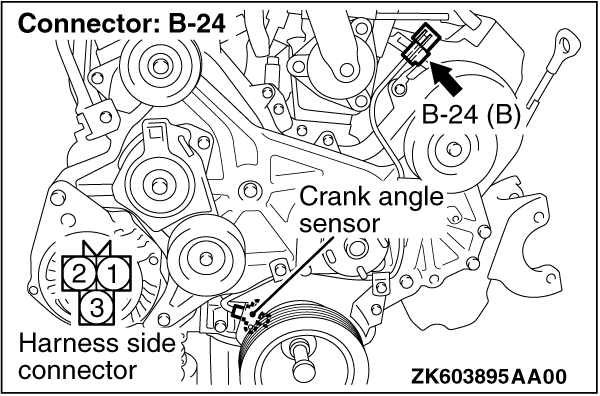
|
- Disconnect connector, and measure at harness side.
- Ignition switch: ON
- Voltage between terminal No. 2 and earth.
OK: 4.9 - 5.1 V
Q.
Is the check result normal? Go to Step 9 .
Go to Step 4 .
|
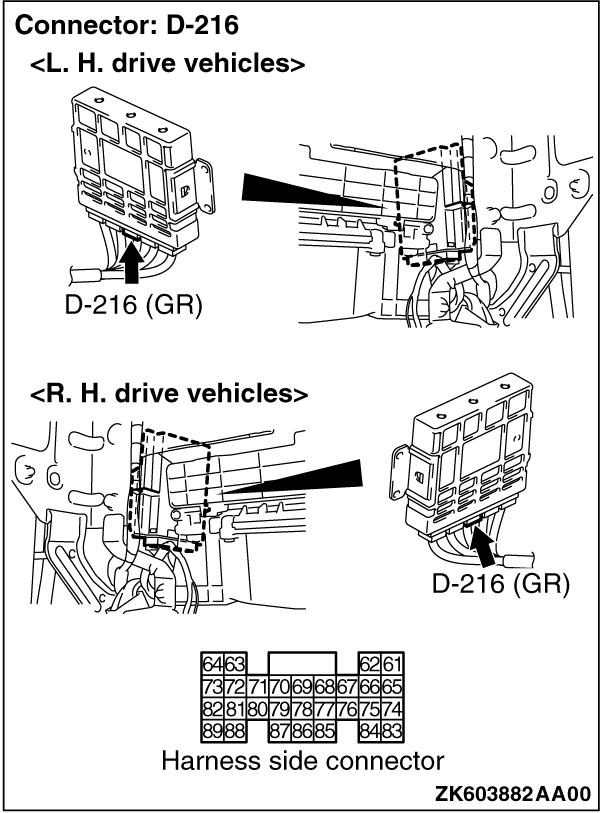
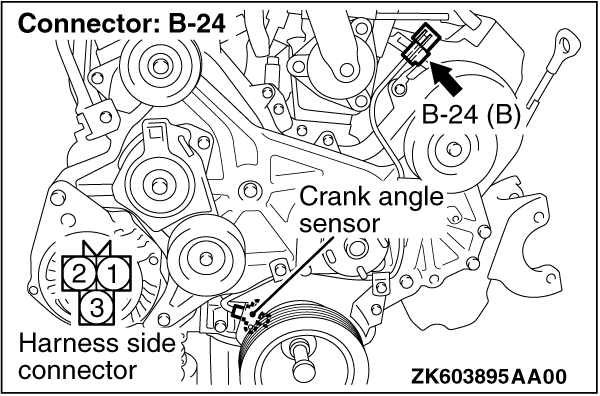
|
- Measure engine-A/T-ECU terminal voltage.
- Disconnect B-24 crank angle sensor connector.
- Ignition switch: ON
- Voltage between terminal No. 70 and earth.
OK: 4.9 - 5.1 V
Q.
Is the check result normal? Go to Step 5 .
Go to Step 6 .
|
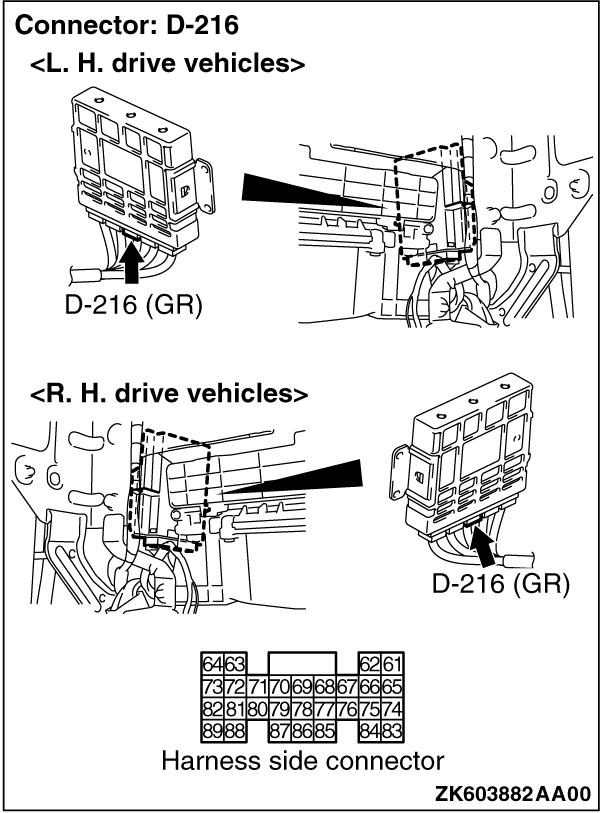
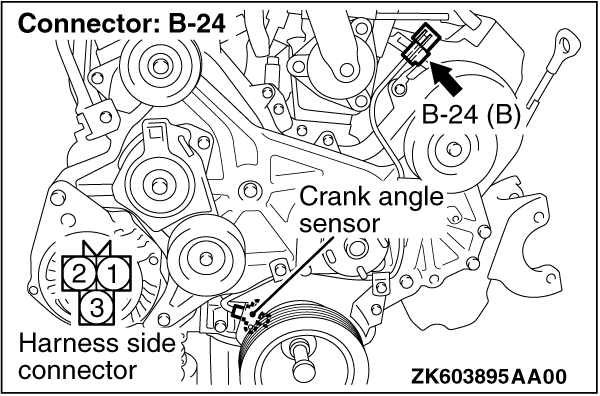
| Q.
Is the check result normal? 
Check and repair harness between B-24 (terminal No.
2) crank angle sensor connector and D-216 (terminal No. 70) engine-A/T-ECU connector.
- Check output line for open circuit.
Repair or replace the connector.
|
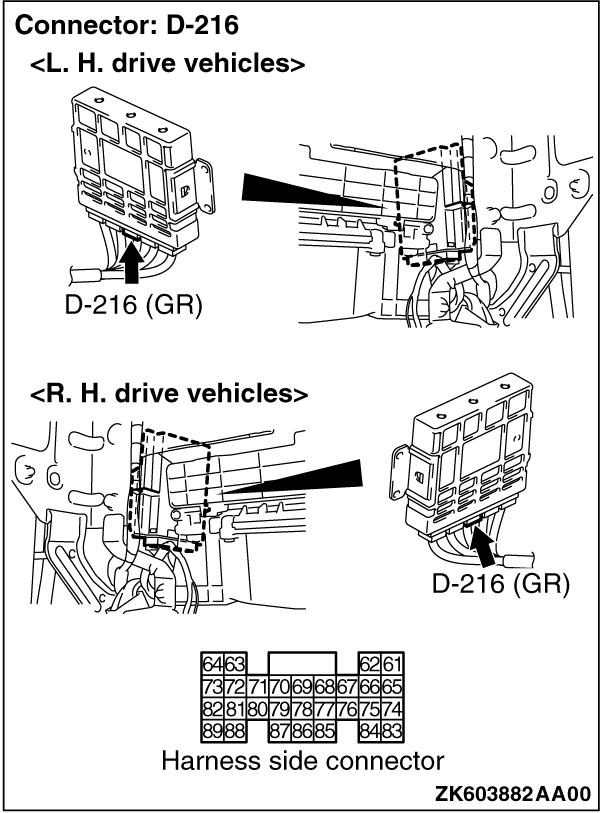
| Q.
Is the check result normal? Go to Step 7 .
Repair or replace the connector.
|
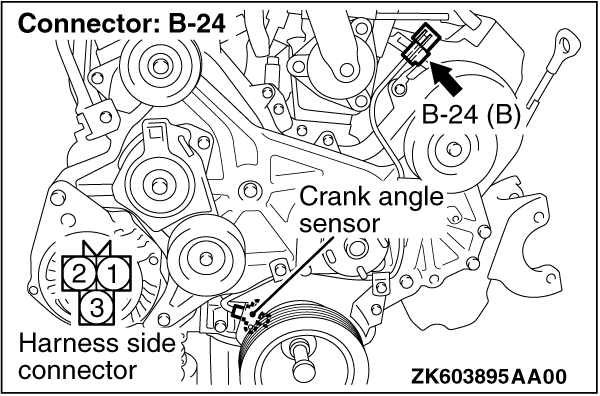
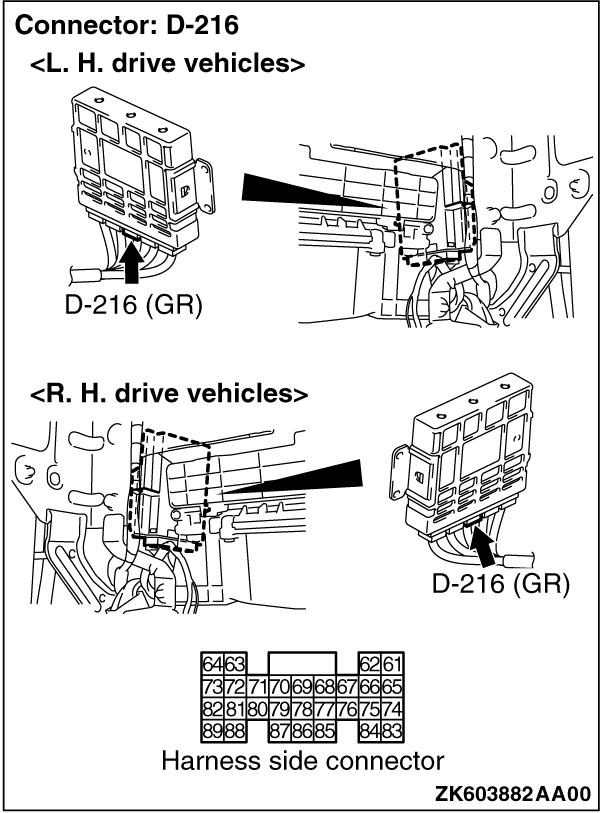
|
- Check output line for short circuit.
Q.
Is the check result normal? Go to Step 8 .
Repair the damaged harness wire.
|
|
- Refer to Data List Reference Table
.
- Item 02: Crank angle sensor
|
| Q.
Is the check result normal? |
| Intermittent malfunction (Refer to GROUP 00 - How to Use Troubleshooting/Inspection
Service Points - How to Cope with Intermittent Malfunctions ).
|
| |
| Replace the engine-A/T-ECU.
|
| |
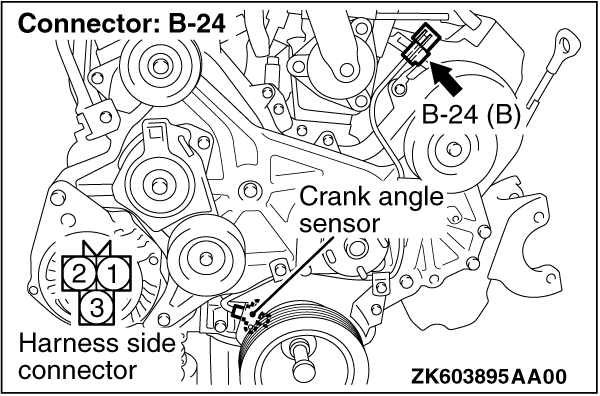
|
- Disconnect connector, and measure at harness side.
- Ignition switch: ON
- Voltage between terminal No. 3 and earth.
OK: System voltage
Q.
Is the check result normal? Go to Step 11 .
Go to Step 10 .
|
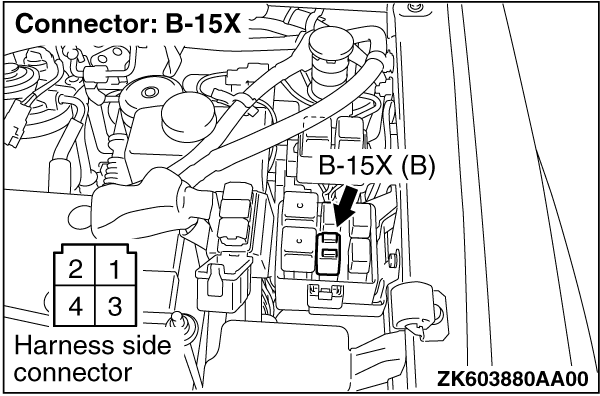
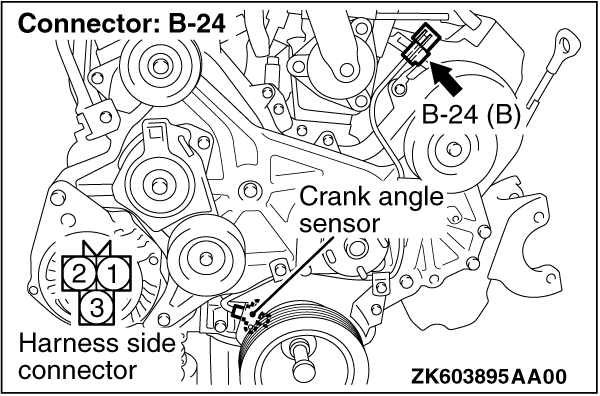
| Q.
Is the check result normal? 
Check and repair harness between B-24 (terminal No.
3) crank angle sensor connector and B-15X (terminal No. 1) engine control relay connector.
- Check power supply line for open/short circuit.
Repair or replace the connector.
|
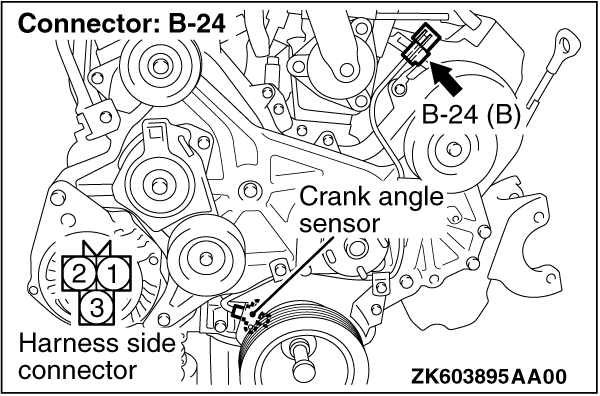
|
- Disconnect connector, and measure at harness side.
- Resistance between terminal No. 1 and earth.
OK: Continuity (2 Ω or less)
Q.
Is the check result normal? Go to Step 14 .
Go to Step 12 .
|
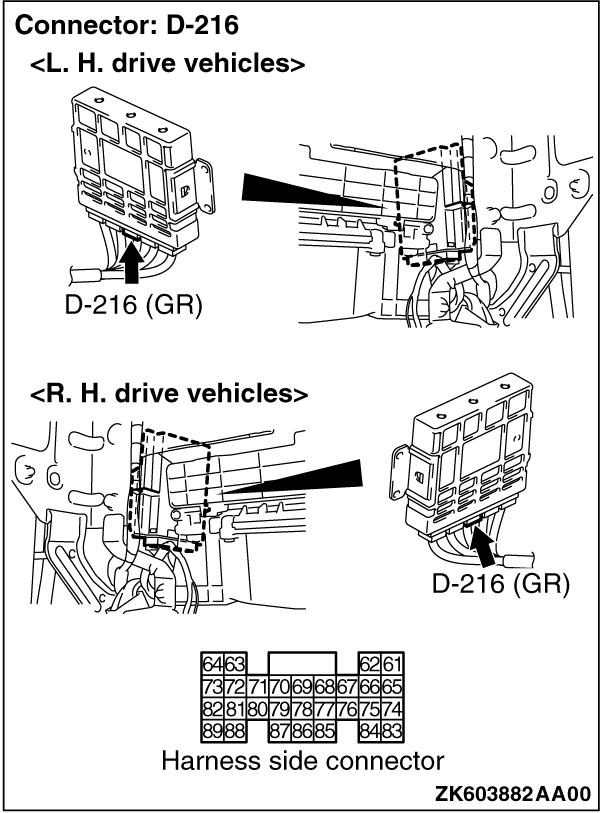
| Q.
Is the check result normal? Go to Step 13 .
Repair or replace the connector.
|
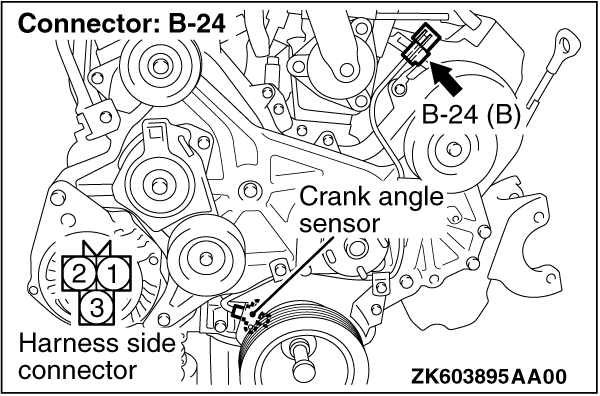
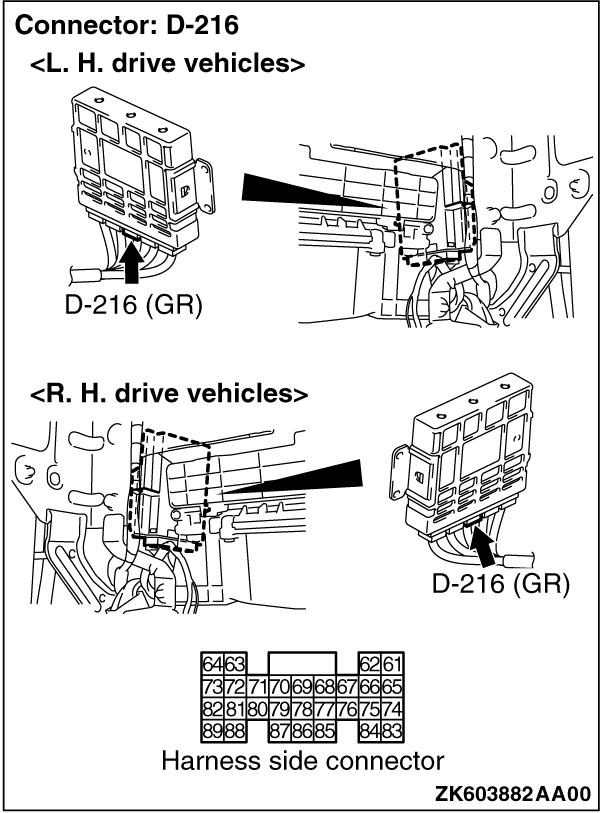
| note | Before checking harness, check intermediate connector D-111, and repair if necessary.
|
- Check earthing line for open circuit and damage.
Q.
Is the check result normal? Go to Step 8 .
Repair the damaged harness wire.
|
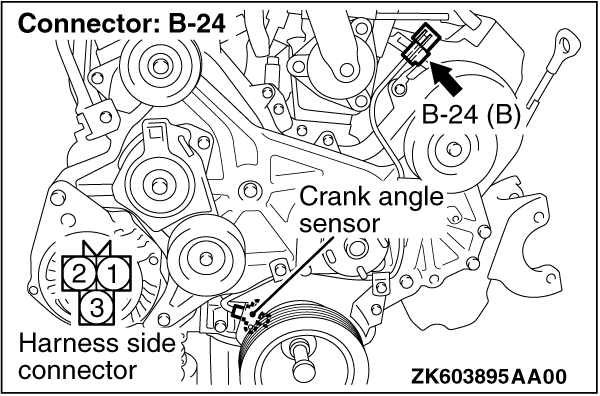
|
- Use special tool test harness (MD998478) to connect connector, and measure
at pick-up harness.
- Engine: Idling
- Transmission: P range
- Voltage between terminal No. 2 and earth.
OK: Waveforms should be displayed on Inspection procedure using an oscilloscope
(Refer to ), its maximum value should be 4.8 V or more,
and its minimum value should be 0.6 V or less with no noise in waveform.
Q.
Is the check result normal? Go to Step 8 .
Go to Step 15 .
|
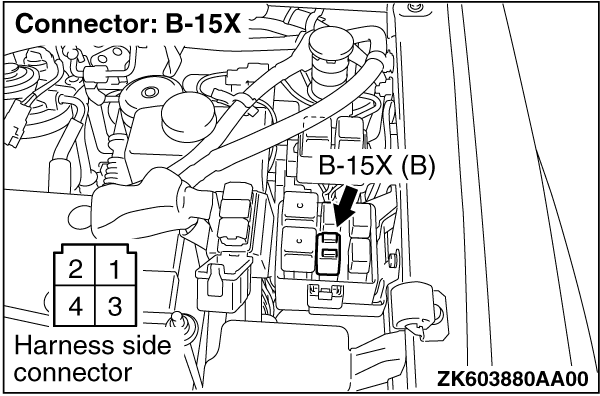
| Q.
Is the check result normal? Go to Step 16 .
Repair or replace the connector.
|
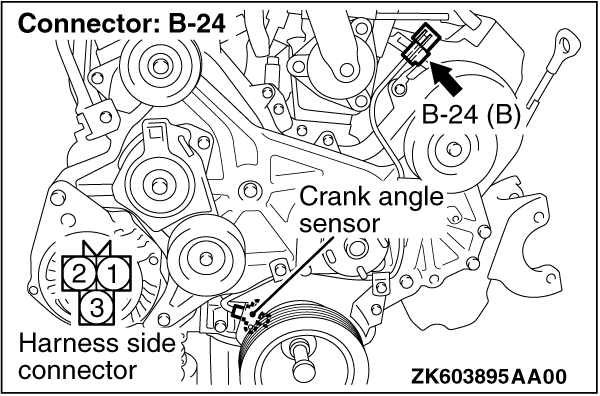
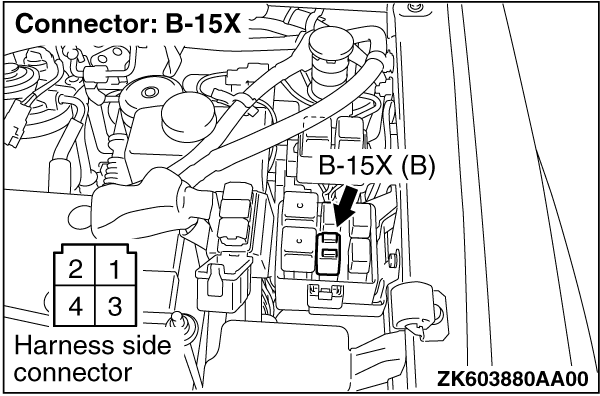
|
- Check power supply line for damage.
Q.
Is the check result normal? Go to Step 17 .
Repair the damaged harness wire.
|
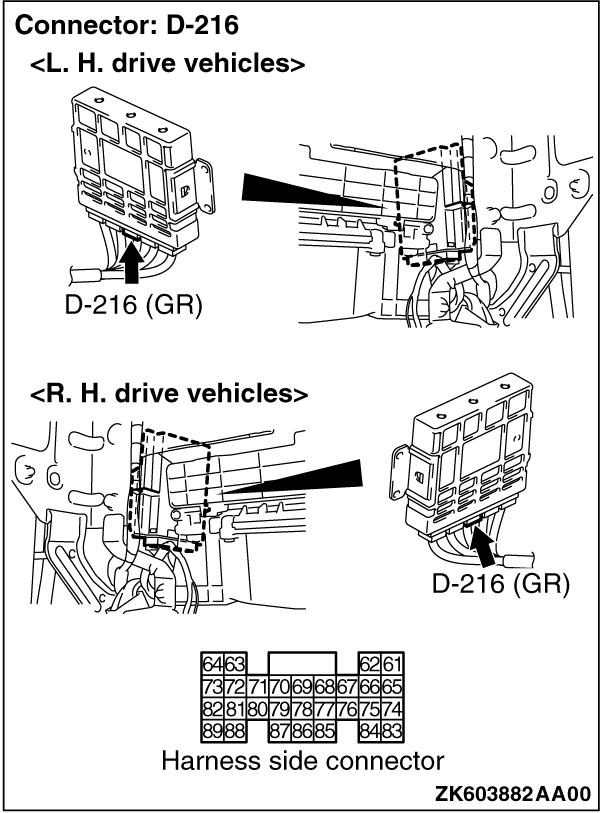
| Q.
Is the check result normal? Go to Step 18 .
Repair or replace the connector.
|
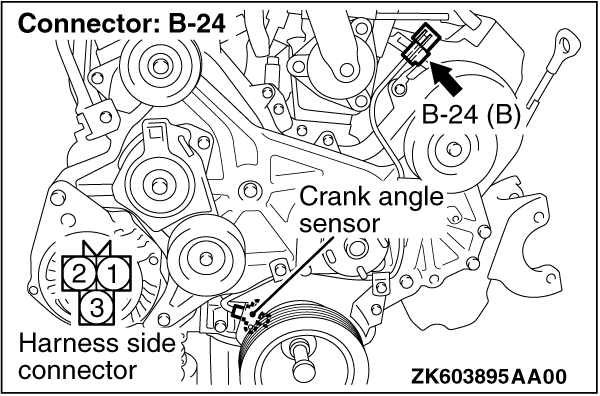
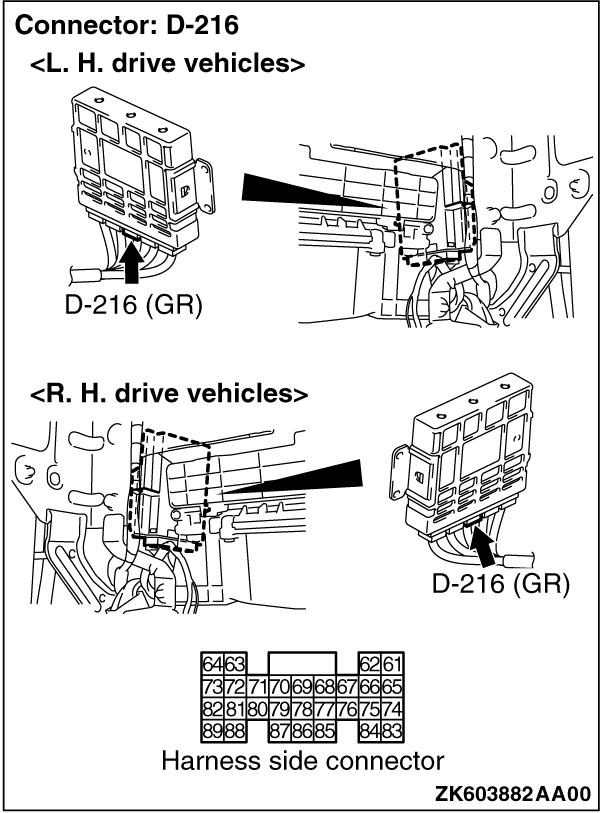
|
- Check output line for damage.
Q.
Is the check result normal? Go to Step 19 .
Repair the damaged harness wire.
|
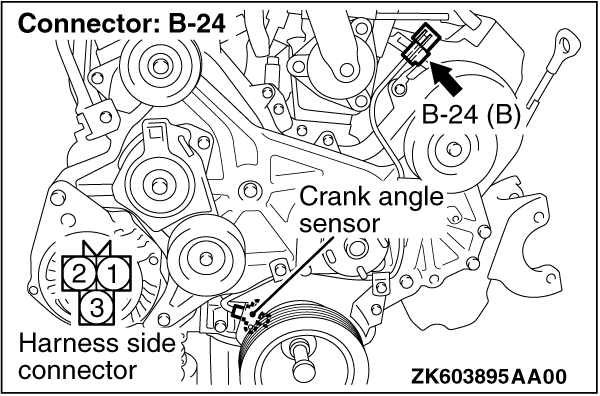
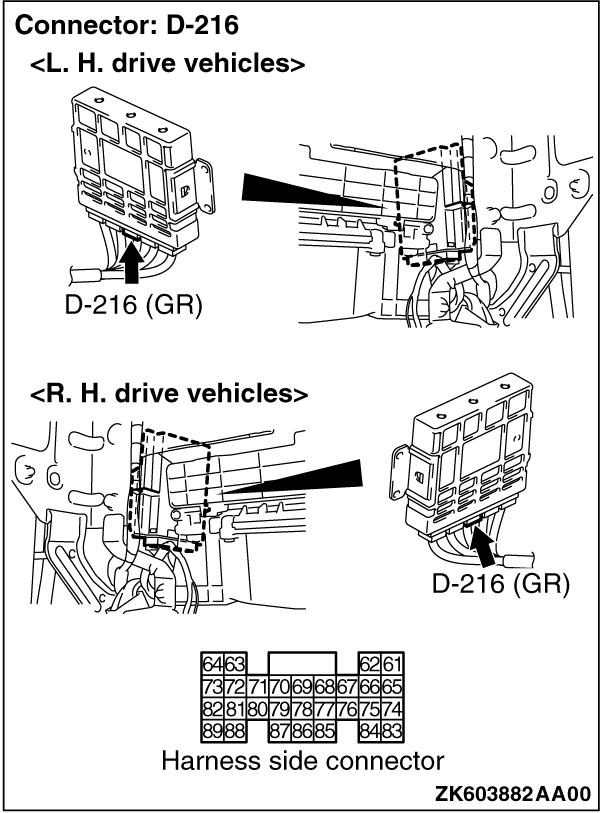
| note | Before checking harness, check intermediate connector D-111, and repair if necessary.
|
- Check earthing line for damage.
Q.
Is the check result normal? Go to Step 20 .
Repair the damaged harness wire.
|
| Q.
Is the check result normal? |
| Replace the crankshaft sensing blade.
|
| |
|
- Refer to Data List Reference Table
.
- Item 02: Crank angle sensor
|
| Q.
Is the check result normal? |
| Intermittent malfunction (Refer to GROUP 00 - How to Use Troubleshooting/Inspection
Service Points - How to Cope with Intermittent Malfunctions ).
|
| |
| Replace the crank angle sensor.
|
| |